熱門(mén)搜索Hot Search
相關(guān)文章推薦
注射件出現(xiàn)裂縫怎么辦?
更新時(shí)間:2020-12-23 14:53:56 次快遞餐飲領(lǐng)域?qū)?a target="_self" title="塑料制品">塑料制品的需求底層拉動(dòng)我國(guó)塑料制品規(guī)模的不斷增長(zhǎng),要想進(jìn)一步深化限塑工作,應(yīng)在減少塑料應(yīng)用的同時(shí)保證快遞餐飲領(lǐng)域?qū)Πb物的需求得到滿足。
注入成形時(shí),聚合物溶體的分子結(jié)構(gòu)排序,在外面力的作用下能造成分子結(jié)構(gòu)鏈的趨向,當(dāng)高分子材料鏈從一種當(dāng)然的平穩(wěn)情況逼迫銜接到另一種趨向情況,最終被鎖定在模貝內(nèi)時(shí),制冷后的塑件便會(huì)造成殘余應(yīng)力。
另外,耐磨材料在冷模誘因溫度差很大,迅速由粘流態(tài)轉(zhuǎn)變?yōu)椴AB(tài),已趨向的生物大分子趕不及修復(fù)原始的平穩(wěn)情況就被鎖定,也使塑件表面殘留了一部分熱應(yīng)力。
一般狀況下,澆口周邊最非常容易產(chǎn)生由殘余應(yīng)力造成的裂紋及裂開(kāi),由于澆口處的成形工作壓力相對(duì)性別的位置要高一些,尤其是流行道為立即澆口時(shí)更是如此。
除此之外,當(dāng)塑件的厚度不勻稱,耐磨材料的制冷速率不一致時(shí),因?yàn)楸『裎恢玫氖諗n量不一樣,前面一種受后面一種的拉申,也會(huì)造成殘余應(yīng)力。因?yàn)闅堄鄳?yīng)力是危害塑件裂紋及裂開(kāi)的一個(gè)關(guān)鍵緣故,因此能夠根據(jù)降低殘余應(yīng)力來(lái)避免 塑件造成裂紋及裂開(kāi)。降低殘余應(yīng)力的關(guān)鍵方式是改善澆筑系統(tǒng)軟件的結(jié)構(gòu)形式和調(diào)節(jié)好塑件的成形標(biāo)準(zhǔn)。
在沖壓模具和制做層面,能夠選用工作壓力損害最少,并且能夠承擔(dān)較高注入工作壓力的立即澆口,可將順向澆口改成好幾個(gè)針式點(diǎn)澆口或側(cè)澆口,并減少澆口直徑。設(shè)計(jì)方案?jìng)?cè)澆口時(shí),可選用成形后可將裂開(kāi)一部分去除的凸片澆口方式。
比如,聚丙稀脂,聚乙烯,聚苯醚等原料的溶體流通性能欠佳,必須在髙壓標(biāo)準(zhǔn)下注入成形,澆口處非常容易造成裂紋,假如選用凸片或側(cè)澆口,可將成形后造成在凸片一部分的裂紋一部分去除。除此之外,在澆口周邊有效選用環(huán)形筋板也可降低澆口處的裂紋。
在加工工藝實(shí)際操作層面,根據(jù)減少注入工作壓力來(lái)降低殘余應(yīng)力是一種最簡(jiǎn)易方式,由于注入工作壓力與殘余應(yīng)力呈正比例關(guān)系。假如塑件表面造成的裂紋四周變黑,即說(shuō)明注入工作壓力太高或投料量太少,盡可能減少注入工作壓力或提升送料量。在模溫及模溫較低的標(biāo)準(zhǔn)下成形時(shí),為使凹模填滿,必定要選用較高的注入工作壓力,導(dǎo)致塑件內(nèi)殘留很多地應(yīng)力。
對(duì)于此事,盡可能提升 料筒及模貝溫度,降低耐磨材料與模貝的溫度差,操縱模內(nèi)型胚的制冷時(shí)間和速率,使趨向的分子結(jié)構(gòu)鏈有較長(zhǎng)的修復(fù)時(shí)間。
除此之外,在確保補(bǔ)料不夠,不使塑件造成收攏凹痕的前提條件下,可適度減少保壓時(shí)間,由于保壓時(shí)間過(guò)長(zhǎng)也非常容易造成殘余應(yīng)力造成裂紋。
外力作用造成 殘余應(yīng)力集中化。
塑料件在出模前,假如出模壓射組織的截面很小或小鏈設(shè)定的總數(shù)不足,小鏈設(shè)定的部位不科學(xué)或安裝歪斜,均衡欠佳,模貝的出模傾斜度不夠,壓射摩擦阻力很大,都是會(huì)因?yàn)橥饬υ斐?應(yīng)力,使塑件表面造成裂紋及裂開(kāi)。
一般狀況下,這類常見(jiàn)故障一直產(chǎn)生在小鏈的周邊。出現(xiàn)這類常見(jiàn)故障后,應(yīng)用心定期檢查校調(diào)壓射設(shè)備。小鏈設(shè)定在出模摩擦阻力較大 的位置,如凸起,筋板等處。
假如設(shè)定的小鏈數(shù)因?yàn)橥祈斂偯娣e遭受標(biāo)準(zhǔn)限定不太可能擴(kuò)張時(shí),可采用用小總面積多小鏈的方式。
假如模貝凹模的出模傾斜度不足,塑件表面也會(huì)出現(xiàn)擦破產(chǎn)生皺褶紋路。在選中出模傾斜度時(shí),務(wù)必考慮到成形原料的縮水率及其壓射系統(tǒng)軟件的構(gòu)造設(shè)定,一般狀況下,出模傾斜度應(yīng)超過(guò)0.85%,中小型塑件的出模傾斜度為0.1~0.5%,大中型塑件的出模傾斜度達(dá)到2.5%。
成形原料與金屬材料鑲件的線膨脹系數(shù)存有差別
因?yàn)闊峁绦运芰系木€膨脹系數(shù)要比不銹鋼板材大9~11倍,比鋁型材大6倍。因而,塑件內(nèi)的金屬材料鑲件會(huì)防礙塑件的整體收縮,從而造成的拉申地應(yīng)力非常大,鑲件四周會(huì)集聚很多的殘余應(yīng)力造成塑件表面造成裂紋。那樣,針對(duì)金屬材料鑲件應(yīng)開(kāi)展加熱,尤其是當(dāng)塑件表面的裂紋產(chǎn)生在剛啟動(dòng)時(shí),絕大多數(shù)是因?yàn)殍偧囟忍蛯?dǎo)致的。
此外,在鑲件材料的采用層面,應(yīng)盡可能選用熱膨脹系數(shù)貼近環(huán)氧樹(shù)脂特點(diǎn)的原材料。比如,選用鋅,鋁等輕金屬原材料制做鑲件好于不銹鋼板材。
在采用成形原料時(shí),也應(yīng)盡量選用高含量的環(huán)氧樹(shù)脂,假如務(wù)必應(yīng)用低含量的成形原料時(shí),鑲件周邊的塑膠薄厚應(yīng)設(shè)計(jì)方案得厚一些,針對(duì)高壓聚乙烯,聚丙稀脂,丙烯酸樹(shù)脂,醋酸纖維素塑膠,鑲件周邊的塑膠薄厚最少應(yīng)相當(dāng)于鑲件直徑的一半;針對(duì)聚乙烯,一般不適合設(shè)定金屬材料鑲件。
原料采用不善或不純粹
不一樣原料對(duì)造成殘余應(yīng)力的敏感性不一樣,一般非結(jié)晶型環(huán)氧樹(shù)脂比結(jié)晶型環(huán)氧樹(shù)脂非常容易造成殘余應(yīng)力造成裂紋;針對(duì)吸水能力環(huán)氧樹(shù)脂及摻用再生顆粒較多的環(huán)氧樹(shù)脂,由于吸水能力環(huán)氧樹(shù)脂加溫后會(huì)溶解老化,較小的殘余應(yīng)力便會(huì)造成脆裂,而再生顆粒成分較高的環(huán)氧樹(shù)脂中殘?jiān)^多,易揮發(fā)性有機(jī)物成分較高,原材料的抗壓強(qiáng)度較為低,也非常容易造成地應(yīng)力裂開(kāi)。
實(shí)踐活動(dòng)說(shuō)明,高粘度松散型環(huán)氧樹(shù)脂不易造成裂紋,因而,在加工過(guò)程中,應(yīng)融合實(shí)際的狀況挑選適合的成形原料。
在操作流程中,脫膜劑針對(duì)耐磨材料而言也是一種臟東西,如使用量不善也會(huì)造成裂紋,應(yīng)盡量避免其使用量。
除此之外,當(dāng)注塑膠機(jī)因?yàn)樯a(chǎn)制造必須拆換原料種類時(shí),務(wù)必把料倉(cāng)上加料器和空氣干燥器中的尾料清除整潔,并列清料筒中的尾料。
塑件總體設(shè)計(jì)欠佳
塑件型體構(gòu)造中的斜角及開(kāi)口處最非常容易造成應(yīng)力,造成 塑件表面造成裂紋及裂開(kāi)。因而,塑件型體構(gòu)造中的外角及內(nèi)角都應(yīng)盡量用較大 半經(jīng)制成弧形。試驗(yàn)說(shuō)明,最好的銜接弧形半經(jīng)為弧形半經(jīng)與拐角處壁厚的比率為1:1.7,即拐角處的弧形半經(jīng)為壁厚的0.6倍。
在設(shè)計(jì)方案塑件的型體構(gòu)造時(shí),針對(duì)務(wù)必設(shè)計(jì)方案成斜角和銳邊的位置依然要選用0.5毫米的最少銜接半經(jīng)制成不大的弧形,那樣能夠增加模貝的使用壽命。
模貝上的裂紋復(fù)映到塑件表面上
在注入成形全過(guò)程中,因?yàn)槟X愒馐茏⑷牍ぷ鲏毫Σ粩喙π?,凹模中具備銳利鈍角的棱邊位置會(huì)造成疲憊裂紋,尤其是在制冷孔周邊尤其非常容易造成裂紋。
當(dāng)模貝與噴頭觸碰時(shí),模貝底端遭受擠壓成型,假如模貝的精準(zhǔn)定位環(huán)孔很大或底壁較薄時(shí),模貝凹模表面也造成疲憊裂紋。
當(dāng)模貝凹模表面上的裂紋復(fù)映到塑件表面處時(shí),塑件表面上造成的裂紋一直以同一樣子在同一位置持續(xù)出現(xiàn)。出現(xiàn)這類裂紋后,應(yīng)該馬上查驗(yàn)裂紋相匹配的凹模表面處是否同樣的裂紋。如果是因?yàn)閺?fù)映功效造成的裂紋,應(yīng)以機(jī)械加工制造的方式恢復(fù)模貝。
相關(guān)文章推薦
技術(shù)熱線(李先生)
134 3149 3911
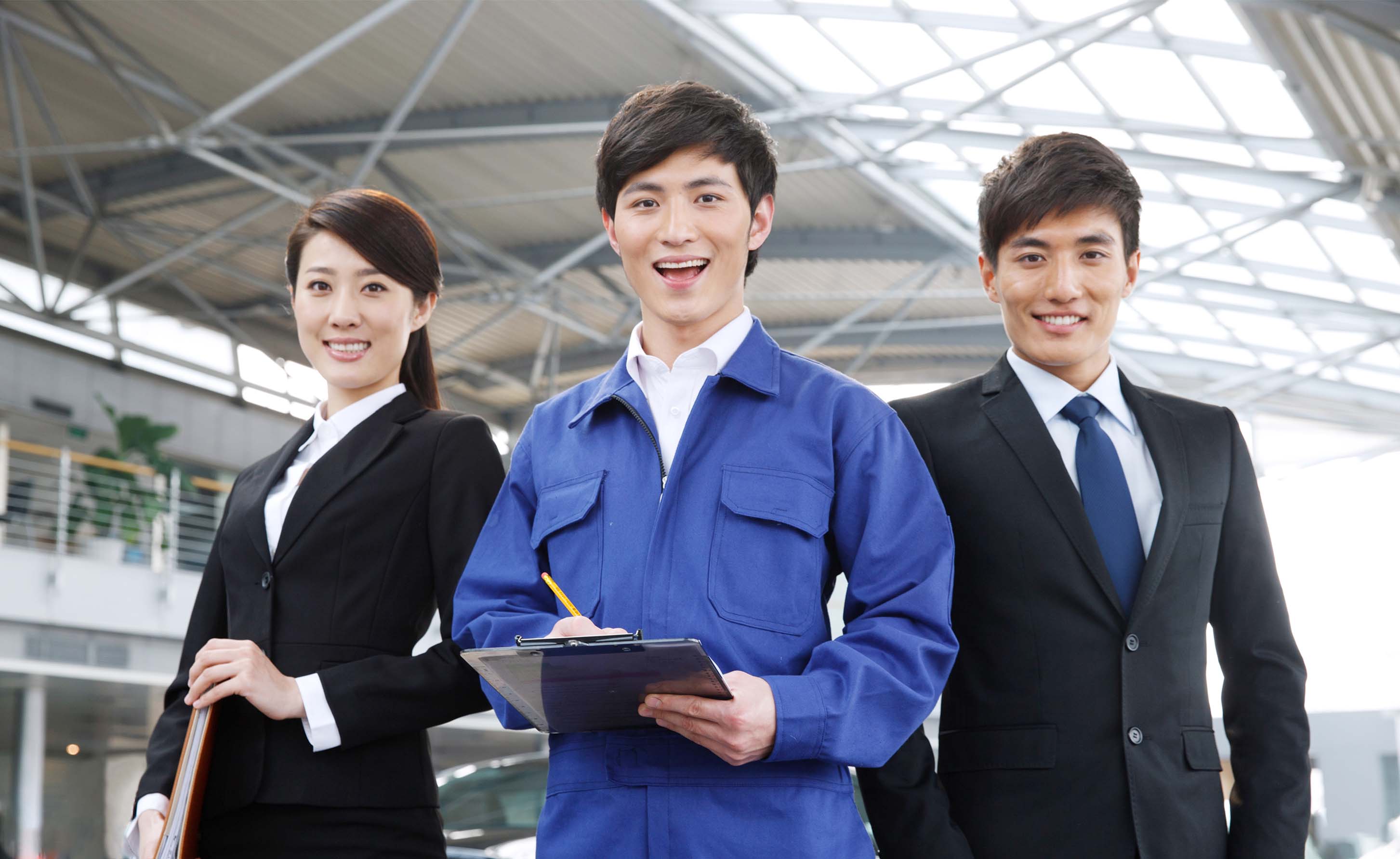